F1

Supply Chain
December 7, 2022
Wake up Call
The global supply-chain crisis exposed catastrophic risks in the system of delivering goods. Will the first responders of tomorrow be men or machines?
Words by Ben Ryder Howe
Photos courtesy David de Vleeschauwer
Long before anyone had heard of COVID-19, Anne Snowdon worried. One of Canada's top healthcare experts, Snowdon spent a lot of time feeling anxious about supply chains, which she thought would be highly vulnerable to breakdown in a calamity such as a pandemic, jeopardizing the delivery of exactly the sort of goods (masks, antibiotics) that would be most needed in an outbreak. Cheerfully but with bracing directness (Snowdon is a former nurse), she told people so—in lectures, journal articles, and hallway conversations with colleagues at the University of Windsor, where she teaches at the business school. Almost no one listened.
“I could give a keynote talk. I could write manuscript after manuscript. It didn't matter. People said, 'You're just fear mongering. It's not that bad.’ And I kept saying back to them, ‘Really?’”
Today, as the global economy struggles to shake off exactly the sort of mass disruption she warned of, Snowdon, who is also chief scientific officer at the Healthcare Information and Management Systems Society, says she takes little comfort in being right, except in one respect:
“People have finally figured out that supply chain matters,” she says. "There's an awareness of the problem, and that alone is a great thing."
But that hasn't stopped her from worrying. On the contrary, she says, the same problems still exist, and “the solution isn't even close at hand.” Moreover, “it's not going to be a small, easy, quick fix.” The supply-chain crisis, the catastrophe lying in plain sight until COVID-19 forced the world to acknowledge it, has the potential to flare up once again even quicker than last time, leaving empty shelves, empty showrooms, stalled ports and crippled economies. That day when you went to the store and saw nothing but blank space where the tampons or toilet paper should have been could recur tomorrow. In fact, the woman who predicted it before sees it as likely.
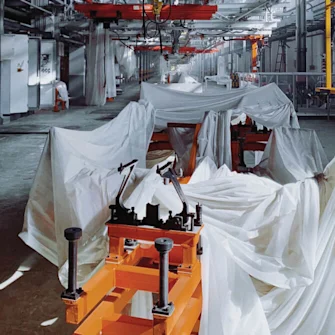
Photography by David de Vleeschauwer
Supply-chain issues are devilishly complex by nature: Goods are delivered on container vessels larger than the Empire State Building, traversing Odyssean shipping routes, yet somehow managing to meet precise, just-in-time deadlines. Such a system is inherently susceptible to paralysis and breakdown, and if the public doesn’t realize it, so much the better from the perspective of producers hoping to provide seamless, friction-free buying experiences.
“Before the pandemic, nobody talked about it except for FedEx, UPS, Amazon and suppliers,” says Jesse Searby, managing partner at Thomas H. Lee Partners, a Boston-based private equity firm with substantial investments in supply-chain-related businesses. “Now it's the topic of every boardroom.”
Snowdon wasn't alone in worrying about it before the pandemic. In 2016, an earthquake struck Taiwan, where nearly all the world’s semiconductors are made, leading to shortages affecting a range of critical industries, from carmakers to Silicon Valley. The recovery was relatively quick, but many saw the incident as a warning. Questions about readiness and the vulnerability of a system balanced on a knife-edge were left unanswered.
“At the end of supply chain is human life,” she says. “My definition of supply chain is who lived, who died. The piece we've been missing is outcomes. And in order to track outcomes, you need a digital automated infrastructure.”
Anne Snowdon Chief Scientific Research Officer at HIMSS
The current, much larger crisis is estimated to have cost the U.S. and European economies up to $4 trillion — in one year. Is the supply-chain crisis a design flaw? Is it a structural phenomenon built into a globalized economy? Are the solutions a matter of summoning the political will, or are they technical and technological? Did the pandemic yield any lessons?
Searby thinks it did. “Before the pandemic,” he says, “we rarely saw machines replacing humans. Now you're seeing more conversation along the lines of, ‘Is it time?’ Companies need predictable labor, and along with the supply-chain crisis we've had a labor shortage. So a lot of folks are making those choices.”
Of course, faced with a choice between a toilet-paper shortage and the rise of the machines, some prefer the security of an older system. It’s a lively debate. Critics contend that even if robots don’t replace humans, they could drive down wages and reduce employee leverage. (Robots never get sick or demand raises.) Supporters, on the other hand, argue that automation is a job creator, increasing productivity and opening markets.
BETA Technologies, a Burlington, Vermont–based startup, shows how cutting-edge supply-chain innovation has the potential to unlock new dimensions of the economy. BETA manufactures battery-powered cargo planes that can take off and land like helicopters and fly the distance between New York City and Boston on a single electric charge. The company has attracted nearly a billion dollars in funding, with investors like Amazon and customers that include UPS, which see the planes as potential green replacements for cargo vans serving the critical “last mile” in the supply chain. The Alia, BETA’s Cessna-size single-engine turboprop, is decidedly human-centered, its cockpit manned by one or two traditional pilots. However, because BETA’s aviation technology represents an entirely new way of flying, thousands of new pilots would have to be trained and employed, adding to an already booming job market.
Moreover, Blain Newton, chief operating officer of BETA, sees the plane as a potential catalyst for opening new regional and local delivery markets. “It’s about moving things through a network,” says Newton. “Ultimately, you're building capacity and transporting more goods. Alia changes the entire topography of that network and allows more throughput to the existing system.”
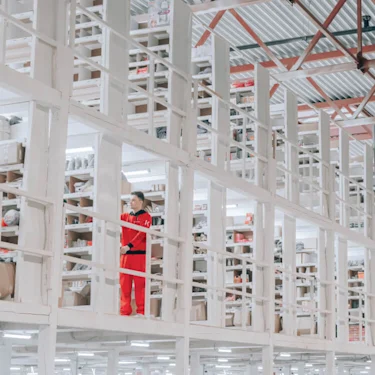
Photography by David de Vleeschauwer
As an example, Newton cites Resonant Link, a “cool little startup” also in Burlington. Resonant Link builds ultra-fast wireless chargers for electric vehicles in medium-duty work roles. “Think of your phone charger, but for a forklift,” says founder Grayson Zulauf. Charging cables operate at sizzling temperatures and are highly susceptible to meltdown, while wireless contact chargers power up more slowly and take up valuable space. Moreover, current technology typically requires a vehicle to go out of service while it recharges.
Resonant Link, on the other hand, is pioneering technology that allows industrial fleets — robots and lift trucks — to power up as they work via charging networks embedded in factory or warehouse floors. Not only does the company’s system make charging easier for operators, but their wireless charging system enables “more throughput” — Zulauf smiles as he says this — “with the same real estate and a smaller number of vehicles, and enables full autonomy as our customers work toward lights-out operation.”
Resonant Link is also using its wireless recharging technology to develop a new generation of medical implants. Newton calls the overlap between healthcare and logistics “huge”: In both areas, he says, the challenge is to increase accuracy through automation.
“Look at smart glasses,” he says. “The technology was used by logistics and manufacturing companies for things like quality control through automatic bar-coding. Then it bled into healthcare settings, where it’s been used to reduce medical error as meds are administered.”
This doesn't go far enough for everyone, however. For Snowdon, fixing the supply chain — if we ever get serious about it — means creating awareness of whether it is succeeding or failing, something the pandemic and all its attendant shortages made progress toward, though not nearly enough.
“At the end of supply chain is human life,” she says. “My definition of supply chain is who lived, who died. The piece we've been missing is outcomes. And in order to track outcomes, you need a digital automated infrastructure.”
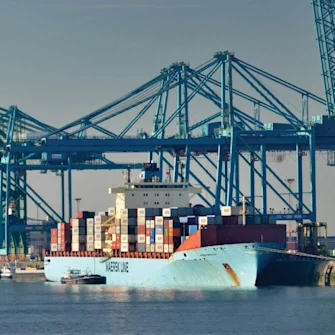
Photography by David de Vleeschauwer
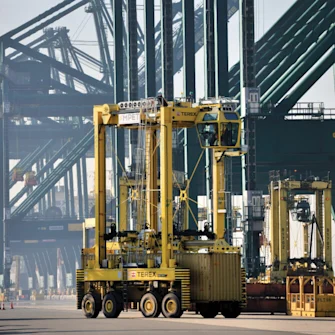
Photography by David de Vleeschauwer
Such an infrastructure would capture vastly more data than the current system, according to Snowdon.
“I can show you several hospital organizations in North America with a high level of digital maturity,” she says. “Can they track and trace every product, every patient who receives that product, every team that delivers the care with that product to an outcome? Almost never. That data infrastructure doesn't exist. We don't have defined outcomes that are measurable or tracked, and therefore we cannot know.”
Does such a system exist anywhere? In Taiwan, every citizen has a personal health record centrally stored in a national database. Health officials look at the records and decide, “OK, here's the 15% of our population most likely to have tragic outcomes with COVID,” says Snowdon. “Before the pandemic they immediately wrapped home-care services around them. As a result, their deaths were in the single digits.”
In the end, it boils down to leadership, says Snowdon. Is supply chain a priority? “If you're the supply-chain lead for an automotive company or an airline manufacturer, you have the corner office overlooking the lake. In healthcare, you're in the basement with a lightbulb hanging out of the ceiling.”
Matthew Verminski, vice president of engineering at Desktop Metal, has spent decades in the supply-chain industry, including in a founding role at Kiva Systems, which became Amazon Robotics, the leading manufacturer of automated storage and retrieval systems in the world. Verminski, too, is cautiously optimistic about overcoming the challenges facing the system.
“There’s a lot we can do, and a lot of people are trying to solve it,” he says. “The challenge is to rebuild manufacturing capabilities in the U.S.,” an area where he points to the leadership of Jeff Wilke, Amazon’s recently departed Worldwide Consumer CEO. Wilke has launched a high-profile, well-funded bid to reinvigorate America’s base of production with Re:Build Manufacturing, a Massachusetts-based company.
“The whole supply chain doesn't need to get rebuilt here,” says Verminski, “but the closer you can get products to people, the better.” He sees “a trend toward local,” whether it’s micro-fulfillment centers or agricultural startups building micro-farms near or even in cities. “There are significant efforts to make advanced technologies happen here.”
Such efforts may end up impacting more than the availability of baby formula at Walmart. Automation has the potential to become the central issue of the coming decades, influencing not just the global economy but reengineering the social fabric. Forward-thinking business leaders such as Wilke, who is credited with growing Amazon from a company generating nearly $4 billion in annual revenue 20 years ago to more than $1 billion a day in 2022, have prioritized onshoring futuristic technologies such as 3D printing and advanced materials partly as a way to ameliorate the disruptions. Of course, technology has a way of proceeding on its own, or making us feel as if it does. But Snowdon says that even if you wanted to, you could never factor humans out of the equation.
“It's always about people and processes,” she says, “then technology.”